<a class="colorbox-inline" href="#popup-content">Click here to see the popup</a> <div style="display: none;"> <div id="popup-content"> <h2>Popup Content</h2> <p>This is the content of the popup.</p> </div> </div>
Operational Excellence: Key Indicators to Improve Efficiency
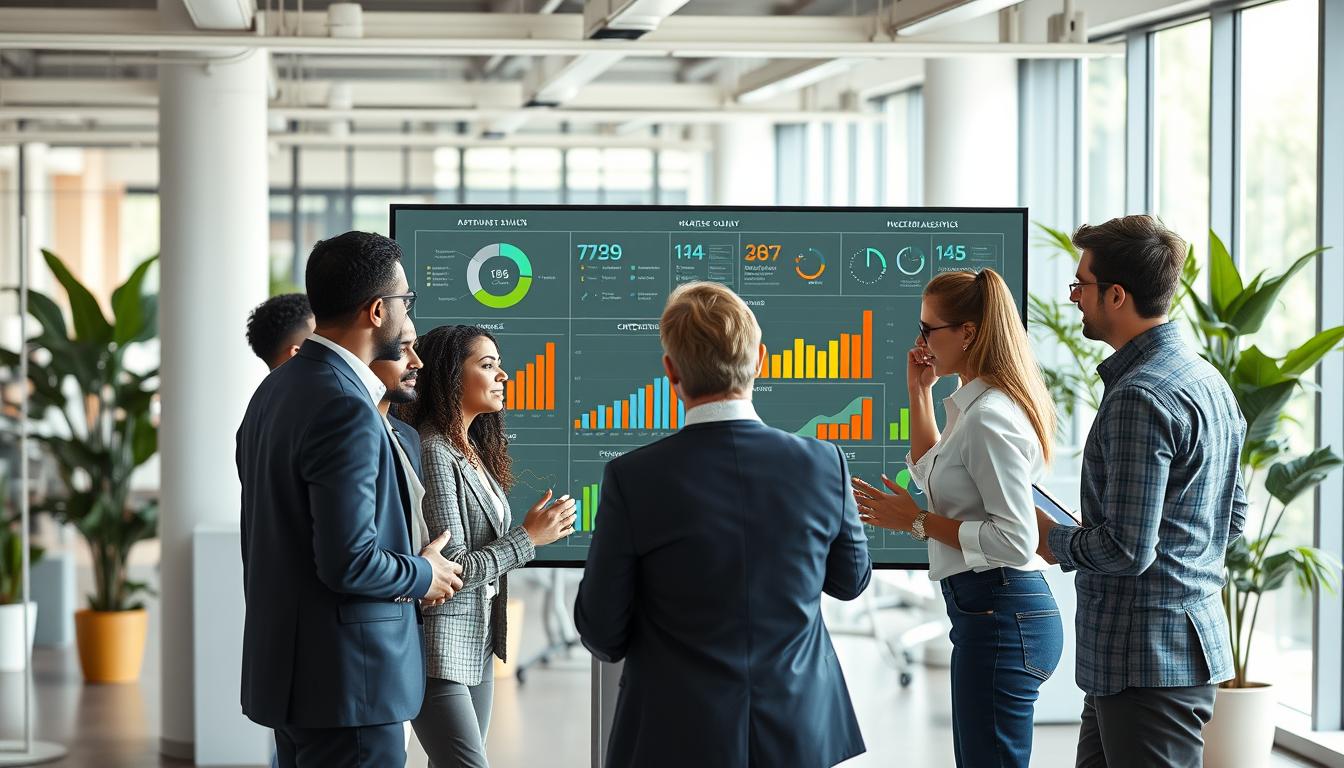
In a highly competitive business world, operational excellence is crucial. By improving processes and reducing waste, companies can operate more efficiently. Adopting a culture of continuous improvement is essential, as it increases productivity and better meets customer satisfaction.
L'excellence opérationnelle vise à rendre les processus plus efficaces en utilisant des méthodes comme le lean management et le six sigma. Ces approches visent à réduire les gaspillages et à améliorer continuellement, grâce à la kaizen.
By implementing methods such as lean management and six sigma, operational excellence aims to reduce waste and continuously improve, or kaizen.
With increased competition and an ever-evolving market, achieving this level of excellence relies heavily on the identification and analysis of key performance indicators. Let's explore the main KPIs to boost operational excellence and ensure optimal results, allowing companies to assess the efficiency of their operations, detect areas for improvement, and make informed decisions.
1. Performance and Productivity
Productivity refers to the efficiency of a facility in optimizing resource use to produce goods or provide a service. This indicator is crucial for understanding the relationship between invested resources (time, labor, raw materials) and the outcomes achieved.
2. Product and service quality
Quality assurance is essential for meeting customer expectations and enhancing their satisfaction.In order to do, quality assurance involves tracking the number of errors or defects in products and services as well as the number of returns.
3. Production Cycle or Processing Time
The importance of improving productivity and quality cannot be overstated. Optimising processes requires an analysis of the value chain and elimination of bottlenecks. It is possible to lose profit and be unable to respond quickly to market demands if the production cycle is too long.
4. Resource Utilization Rate
The resource utilization rate measures the efficiency with which equipment, facilities, or employees are used. This indicator identifies periods of inactivity or underutilization of resources.
5. Operating Costs
Operating costs include all expenses related to production, such as wages, raw materials, energy, and machine maintenance. Tracking these costs helps identify savings opportunities and optimize the budget.
6. Customer satisfaction
Customer satisfaction is a key indicator for understanding how well products and services meet market expectations. It is often measured through satisfaction surveys or customer feedback analysis.
To achieve long-term excellence, it’s essential to invest in team training and involve employees in continuous improvement efforts. This strategy, grounded in continuous learning and agile leadership, fosters an innovative and high-performing corporate culture.
Need help or advice on improving your operational efficiency? Contact us for more information and discover how we can support you in achieving operational excellence.